
EV 600
- Anodized ALU profile structure (thickness 15 Microns) Alloy 6060
- Standard configuration complete with:
– Polycarbonate tunnel to protect the elevator lane
– Elevator hopper in 2 mm thick AISI 304 stainless steel sheet
– Elevator unloading chute in aluminium complete with internal lining applied to the surface in contact with the product
– Padlockable switch/motor protector + cable and plug - Standard cut-proof, oil-proof belt with smooth green Polyurethane covering (ref. Pantone 320) and h 30 mm heat-welded slats at 150 mm pitch; vulcanized belt joint
- Temperature resistance: from -10 to +90°C
- Power: 0,12 kW
- Speed: 12 m/min fixed
- Voltage: 400 V / 50 Hz
- Std installation: on left-hand side so as to exercise a thrusting action, fixed drive with shaft-mounted flange
- Worm reduction gear with life-long lubrication
- Hopper in brushed AISI 304 stainless steel complete with Polycarbonate cover
- Food-grade white belt
- Unloading chute and side panels entirely made of AISI 304 stainless steel
STANDARD DIMENSIONAL FEATURES

CONFIGURATIONS

EV - HOPPER WITH RAPID UNLOADING ACTION
- Detail of the rapid unloading device, which can be installed on the hopper as an optional
- The manually opened damper allows residues of product to be removed from the bottom of the hopper or samples to be taken for quality control purposes
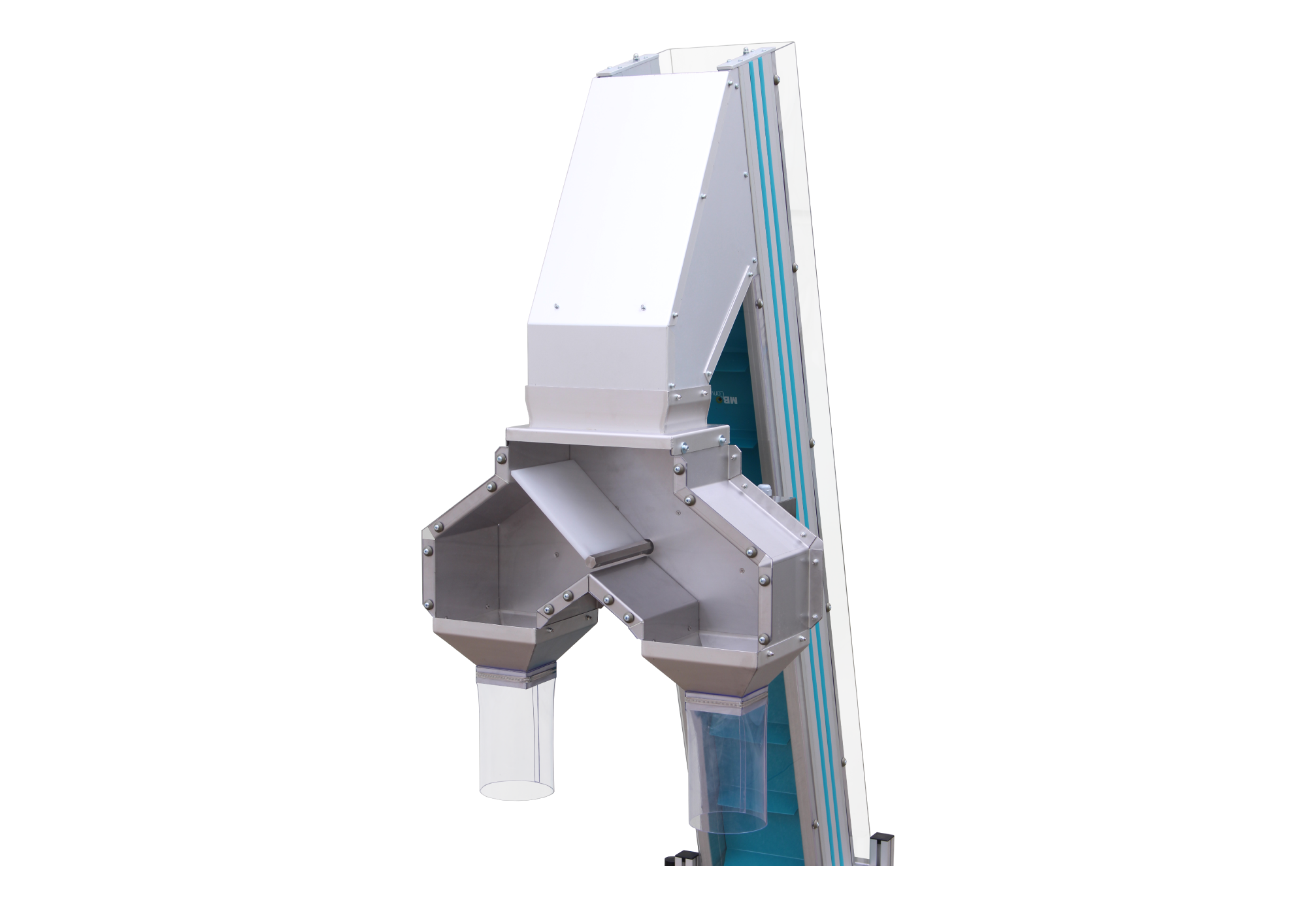
EV COMPLETE WITH TWIN OUTFEEDS
- The photo alongside shows a twin outfeed installed on an elevator
- In this case, the twin outfeed is installed directly at the outlet of the standard chute supplied with the elevator
- The standard centre distances proposed between one outfeed track and the other are: L 600 or L 800 mm
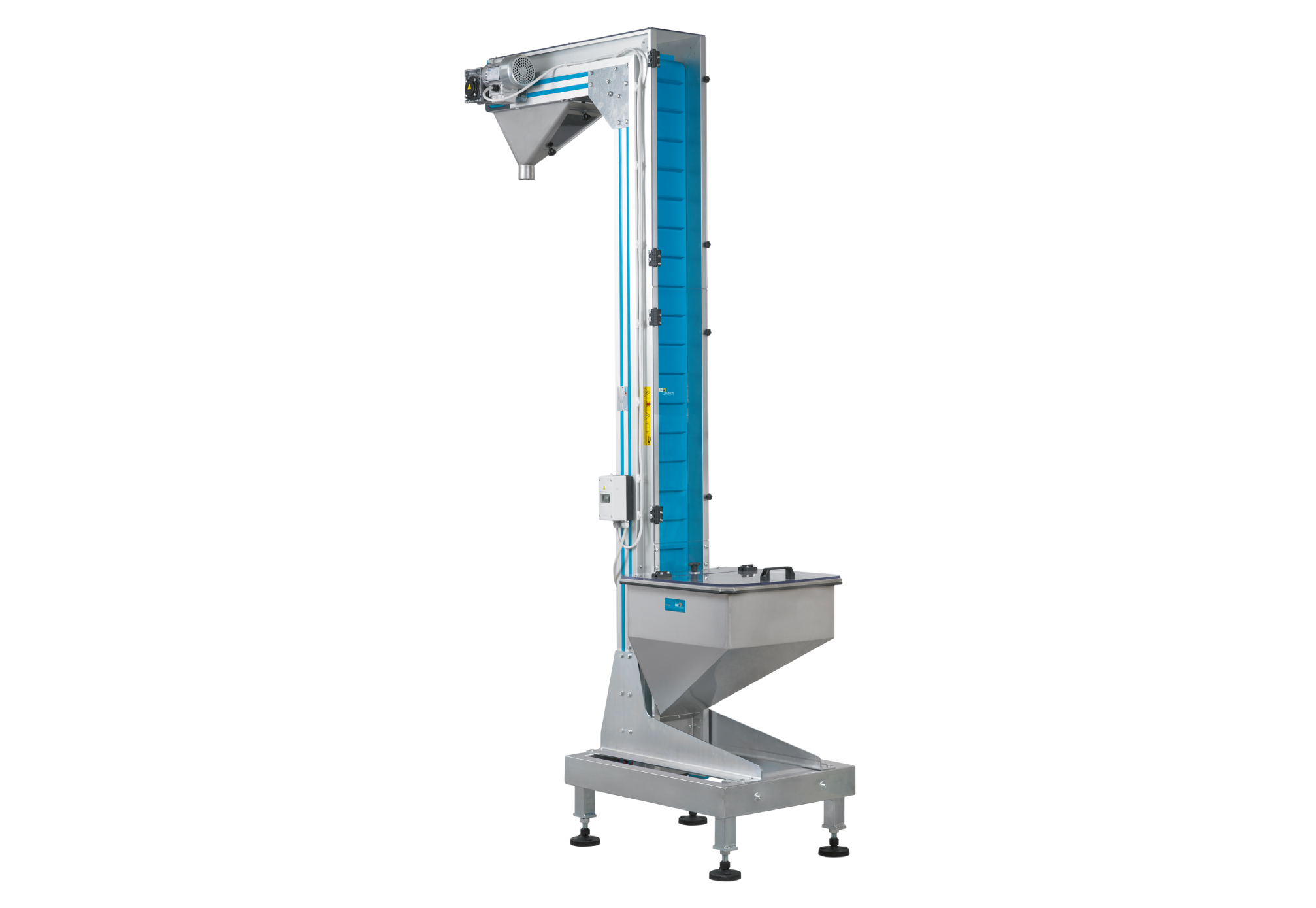
EV WITH VERTICAL SECTION AND FLAT UPPER SECTION
- This photo illustrates a solution which can be proposed when there is not much room for the elevator
- The degree of functionality achieved by the elevator in this configuration depends on the type of product in question (the product must be examined before this solution can be proposed)
- The photo shows the funnel-shaped unloading chute that accurately channels the product inside the assembling unit

EV - DETAIL OF HOPPER COVERING
- The loading hopper in the photo alongside has a Polycarbonate cover. This is only installed as standard equipment on elevators for food products and pharmaceuticals. It is available as an optional on conventional conveyors
- The cover can be provided complete with hinges and/or gas springs to ensure it remains safely in any position
- The cover can be strengthened by a tubular aluminium frame (recommended when the hopper is very large – 1000/1200 mm)

EV - ACCESSORIES
- The photo alongside shows the level sensor complete with MB control panel
- The MB control panel installed in conjunction with the sensor has the following standard functions:
– when in the vertical position (see photo), the sensor rod signals that there is no product downline: the panel transmits a Start signal to the elevator
– in the horizontal position, the sensor signals to the panel that there is an abundance of product downline: the panel transmits a Stop signal to the elevator
– the Start and Stop signals are only transmitted to the MB control panel after the time required to ascertain the actual need

EV COMPLETE WITH PRODUCT HANDLER
- MB proposes the solution illustrated in the photo alongside when the product tends to create a “bridge” effect owing to its conformation
- The white section of the hopper has a pneumatic pusher which determines its vertical movement towards the product in the hopper, thereby preventing the “bridge” effect

EV - HOPPER WITH RAPID UNLOADING ACTION
- Detail of the rapid unloading device, which can be installed on the hopper as an optional
- The manually opened damper allows residues of product to be removed from the bottom of the hopper or samples to be taken for quality control purposes
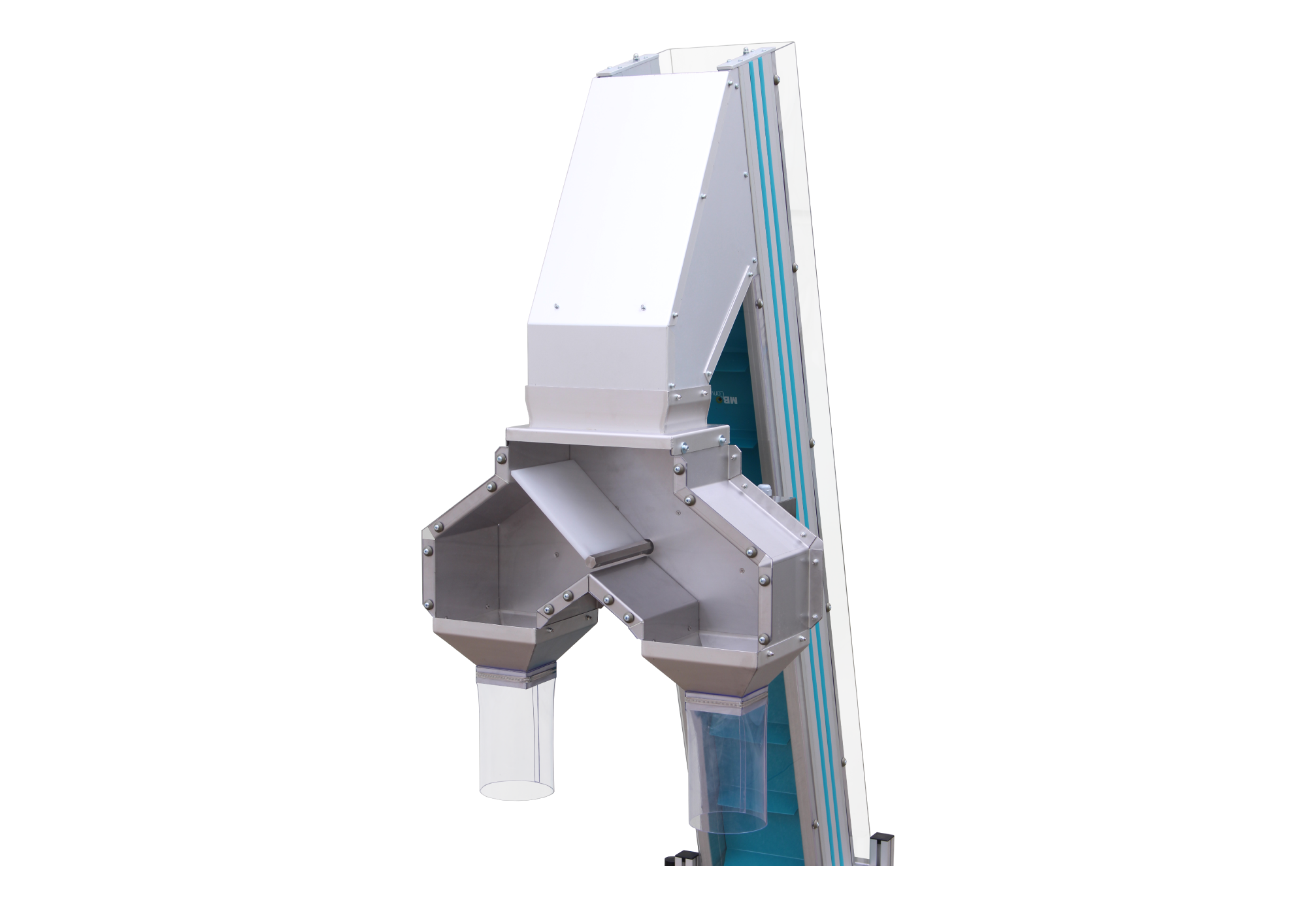
EV COMPLETE WITH TWIN OUTFEEDS
- The photo alongside shows a twin outfeed installed on an elevator
- In this case, the twin outfeed is installed directly at the outlet of the standard chute supplied with the elevator
- The standard centre distances proposed between one outfeed track and the other are: L 600 or L 800 mm
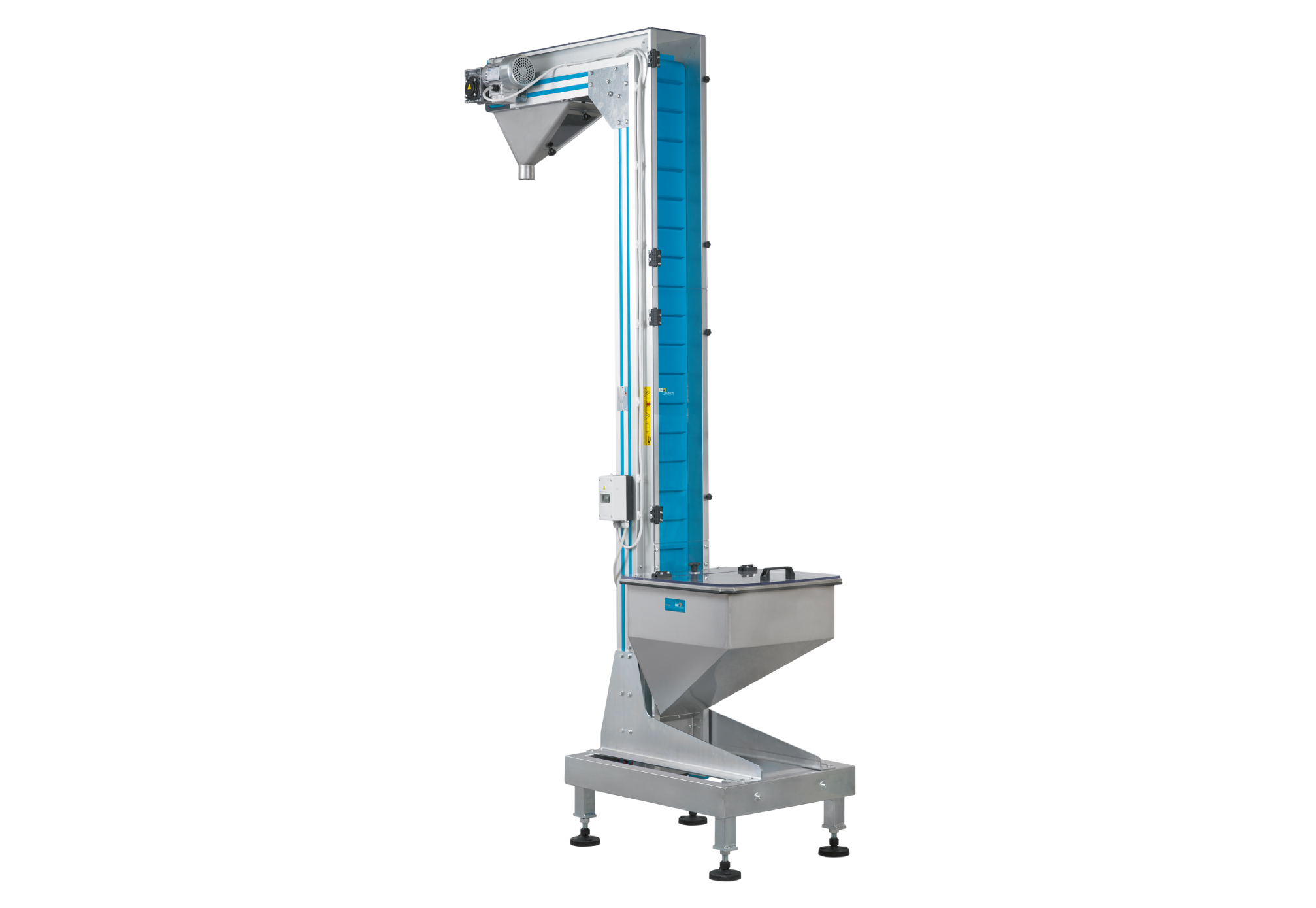
EV WITH VERTICAL SECTION AND FLAT UPPER SECTION
- This photo illustrates a solution which can be proposed when there is not much room for the elevator
- The degree of functionality achieved by the elevator in this configuration depends on the type of product in question (the product must be examined before this solution can be proposed)
- The photo shows the funnel-shaped unloading chute that accurately channels the product inside the assembling unit

EV - DETAIL OF HOPPER COVERING
- The loading hopper in the photo alongside has a Polycarbonate cover. This is only installed as standard equipment on elevators for food products and pharmaceuticals. It is available as an optional on conventional conveyors
- The cover can be provided complete with hinges and/or gas springs to ensure it remains safely in any position
- The cover can be strengthened by a tubular aluminium frame (recommended when the hopper is very large – 1000/1200 mm)

EV - ACCESSORIES
- The photo alongside shows the level sensor complete with MB control panel
- The MB control panel installed in conjunction with the sensor has the following standard functions:
– when in the vertical position (see photo), the sensor rod signals that there is no product downline: the panel transmits a Start signal to the elevator
– in the horizontal position, the sensor signals to the panel that there is an abundance of product downline: the panel transmits a Stop signal to the elevator
– the Start and Stop signals are only transmitted to the MB control panel after the time required to ascertain the actual need

EV COMPLETE WITH PRODUCT HANDLER
- MB proposes the solution illustrated in the photo alongside when the product tends to create a “bridge” effect owing to its conformation
- The white section of the hopper has a pneumatic pusher which determines its vertical movement towards the product in the hopper, thereby preventing the “bridge” effect