
SOFT DROP
CONTAINER FILLING DEVICE FOR PREFORMS
- Anodized ALU profile structure (thickness 15 Microns) Alloy 6060 90×90 mm
- FootMaster ground supports: a single device allows both locking to the ground and quick and safe handling in case of need
- Standard Soft Drop complete with control unit with Touch panel installed on the side for an easier and safer access, to control the operating process via PLC:
– work cycles and parameter settings displayed
– monitoring of the quantity of preforms placed in the containers by counting the moulding cycles of the production unit - Power required (including loading CPT): 1 kW
- Standard voltage: 400 Volt / 50 Hz
- Compressed air: flow rate 610 litres/minute (36,6 m3/h) – pressure 600/800 kPA (6 Bars)
- Optionals:
– quality control by weighing the preforms per container with 0 to + 2% tolerance
– installation of vibrating platforms
– cooling device on loading conveyor
– Ethernet remote assistance
- The product from the moulding cycle is accumulated on the press and channelled by a mod. CPT conveyor to the mod. PA conveyor/distributor installed for programmed filling of the hoppers/lowerators
- Once the loading phase has terminated, the hopper descends into the container and, using an ultrasound sensor, releases the preforms at a minimum predefined height
- When the first container has been filled, filling of the second container begins, while an audible-visual alarm warns the operator that the filled container must be replaced with an empty one
- “Soft” storage of products in the containers
- The quantity of products in the container is controlled by counting the IMM cycles or, on request, by weighing
- Suitable types of containers (max dim. 1200x1200mm):
– Octabins
– Plastic containers
– Metal mesh crates
Up To 40,000
Preforms/H
Vertical axis drive
Pneumatic

STANDARD DIMENSIONAL FEATURES

POSITIONING EXAMPLES
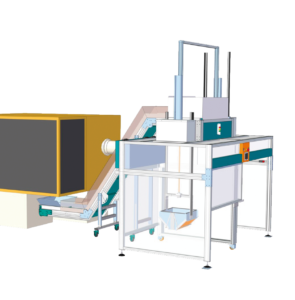
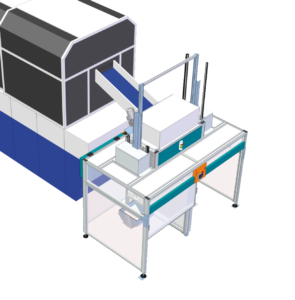
SOFT DROP APPLICATION WITH FEEDING CONVEYOR
- In this application, the preforms are received by the conveyor inside the press positioned under the mould opening
- The dimensional features of the accumulation conveyor depend on:
– press model used
– production capacity of press
– dimensions of preforms
SOFT DROP APPLICATION WITHOUT FEEDING CONVEYOR
- The drawing alongside shows the Soft Drop receiving the preforms directly from the conveyor provided for the press
- The dimensional and functional features of the Soft Drop are standard, except for the casing installed on the distributor conveyor which receives the preforms.
- The control panel and operating logic are standard
CONFIGURATIONS

FOUR-POSITION SOFT DROP
- The photo alongside illustrates a special solution designed for filling four different containers with preforms instead of the usual two
- In this application, the quantity of preforms to be placed in the container is controlled by weighing
- Vibrating platforms controlled by the main control panel complete the system

FOUR-POSITION SOFT DROP - REAR VIEW
- The photo alongside shows a mod. CPT conveyor, which receives preforms from the production unit, the conveyor leading to the Soft Drop and the system of flat belt conveyors for distributing preforms among four different unloading stations
- Note the control panel installed on the conveyor, used for managing the system

SOFT DROP WITH SOUNDPROOFING
- The Soft Drop in the photo alongside has been fitted with soundproofing panels
- This type of solution is proposed when metal cages are used for collecting the preforms

SOFT DROP WITH WEIGHING SYSTEM
- High-precision weighing systems can be installed on MB Soft Drop devices, allowing the contents of the octabins into which the preforms are placed (from 0 to +8 preforms) to be accurately determined
- Thanks to the exclusive MB design, the weighing system on these Soft Drops can be used in conjunction with vibrating devices to optimize the filling process and obtain the best performance from the system

SOFT DROP LOADING BELT WITH COOLING SYSTEM
- The photo alongside shows a series of Soft Drops in which, on the CPT loading conveyor, a system with helical fans for rapid cooling of the preforms has been installed
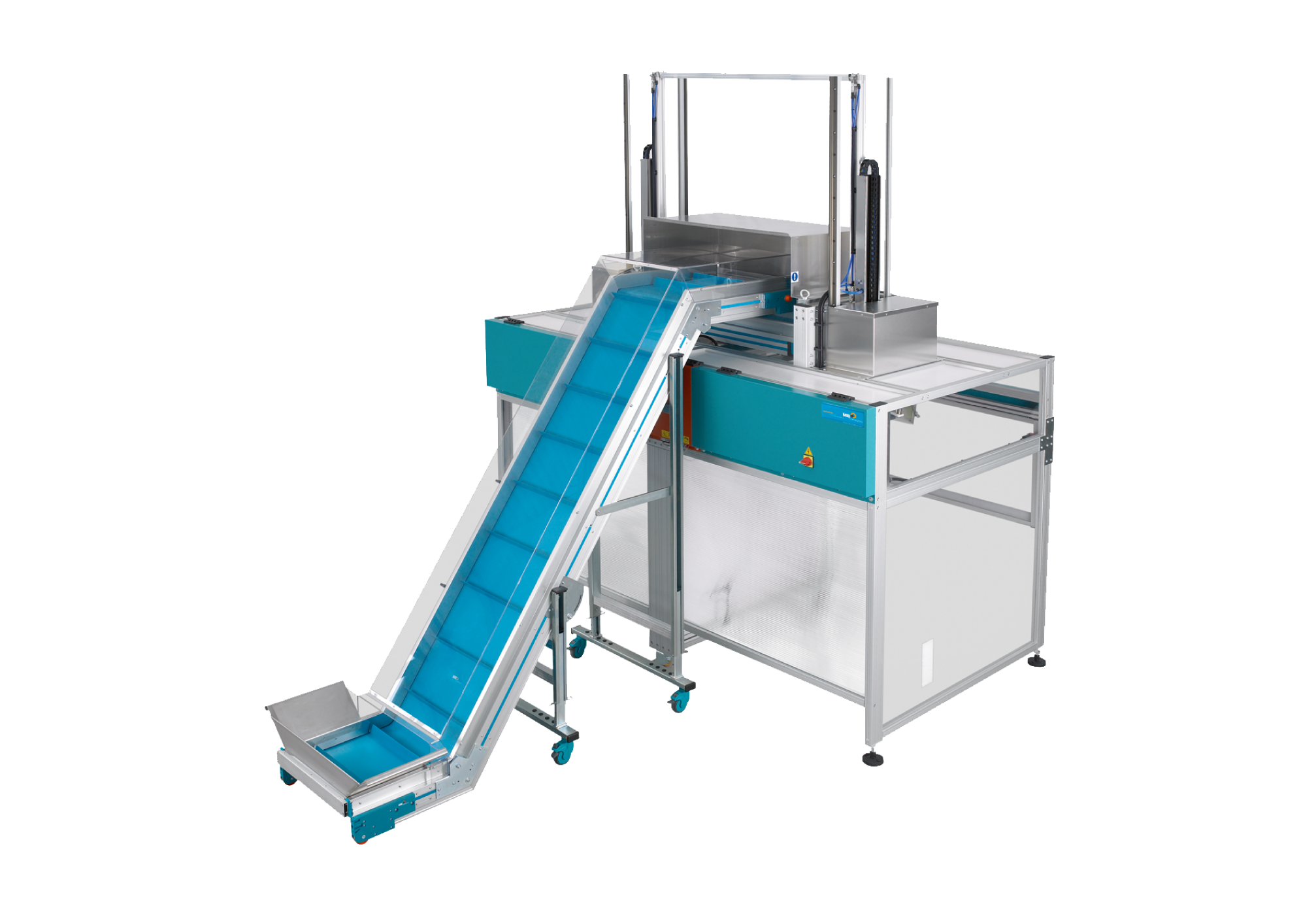
STANDARD SOFT DROP – REAR VIEW
- The mod. CPT standard loading conveyor:
– receives the preforms at the production outlet and channels them to the mod. PA conveyor/distributor installed on the Soft Drop
– green PU belt (ref. Pantone 320) complete with h 50 mm slats, pitch 300 mm; vulcanized belt joint
– 17 m/min fixed conveyor speed
– 55° inclination of upward section
– Polycarbonate guard along the entire length of the conveyor

DETAIL OF PREFORM COLLECTING, LOWERING AND OUTFEEDING HOPPER
- The photo alongside shows the hopper which receives the preforms from the mod. PA conveyor/distributor
- The hopper is provided with a pneumatic system for vertical descent into the container
- The hopper bottom consists of two panels with pistons, which open when the release height is reached

DETAIL OF HOPPER WITH OPEN PANELS
- Panel opening can be set according to different logic sequences:
–simultaneous opening of the panels
– opening of the right-hand panel during the first descent and the left-hand panel during the second descent
– opening of both panels but at different times - Note the ultrasound proximity sensor which determines panel opening

STANDARD TOUCH PANEL WITH SIEMENS S7-1200 SERIES PLC
- The system is controlled by a PLC with colour Touch Screen and user-friendly interface for simple settings and ease of use

FOUR-POSITION SOFT DROP
- The photo alongside illustrates a special solution designed for filling four different containers with preforms instead of the usual two
- In this application, the quantity of preforms to be placed in the container is controlled by weighing
- Vibrating platforms controlled by the main control panel complete the system

FOUR-POSITION SOFT DROP - REAR VIEW
- The photo alongside shows a mod. CPT conveyor, which receives preforms from the production unit, the conveyor leading to the Soft Drop and the system of flat belt conveyors for distributing preforms among four different unloading stations
- Note the control panel installed on the conveyor, used for managing the system

SOFT DROP WITH SOUNDPROOFING
- The Soft Drop in the photo alongside has been fitted with soundproofing panels
- This type of solution is proposed when metal cages are used for collecting the preforms

SOFT DROP WITH WEIGHING SYSTEM
- High-precision weighing systems can be installed on MB Soft Drop devices, allowing the contents of the octabins into which the preforms are placed (from 0 to +8 preforms) to be accurately determined
- Thanks to the exclusive MB design, the weighing system on these Soft Drops can be used in conjunction with vibrating devices to optimize the filling process and obtain the best performance from the system

SOFT DROP LOADING BELT WITH COOLING SYSTEM
- The photo alongside shows a series of Soft Drops in which, on the CPT loading conveyor, a system with helical fans for rapid cooling of the preforms has been installed
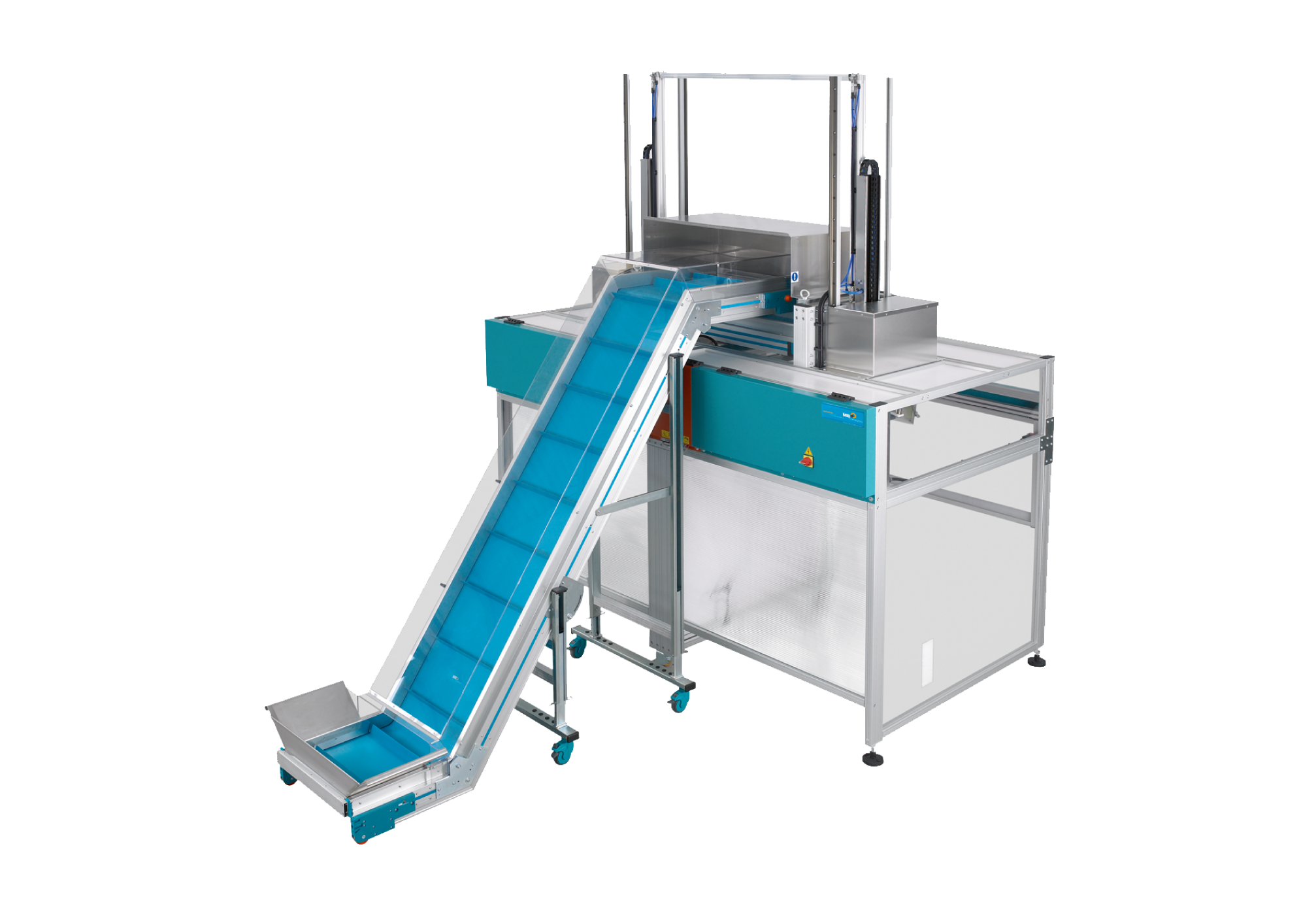
STANDARD SOFT DROP – REAR VIEW
- The mod. CPT standard loading conveyor:
– receives the preforms at the production outlet and channels them to the mod. PA conveyor/distributor installed on the Soft Drop
– green PU belt (ref. Pantone 320) complete with h 50 mm slats, pitch 300 mm; vulcanized belt joint
– 17 m/min fixed conveyor speed
– 55° inclination of upward section
– Polycarbonate guard along the entire length of the conveyor

DETAIL OF PREFORM COLLECTING, LOWERING AND OUTFEEDING HOPPER
- The photo alongside shows the hopper which receives the preforms from the mod. PA conveyor/distributor
- The hopper is provided with a pneumatic system for vertical descent into the container
- The hopper bottom consists of two panels with pistons, which open when the release height is reached

DETAIL OF HOPPER WITH OPEN PANELS
- Panel opening can be set according to different logic sequences:
–simultaneous opening of the panels
– opening of the right-hand panel during the first descent and the left-hand panel during the second descent
– opening of both panels but at different times - Note the ultrasound proximity sensor which determines panel opening

STANDARD TOUCH PANEL WITH SIEMENS S7-1200 SERIES PLC
- The system is controlled by a PLC with colour Touch Screen and user-friendly interface for simple settings and ease of use

FOUR-POSITION SOFT DROP
- The photo alongside illustrates a special solution designed for filling four different containers with preforms instead of the usual two
- In this application, the quantity of preforms to be placed in the container is controlled by weighing
- Vibrating platforms controlled by the main control panel complete the system
Category: PET