
SR
INDEPENDENT SEPARATOR WITH ROLLER DRUM
- Standard: 24 rollers in PVC ø 50 mm length 800 mm
- Standard equipment:
– MB Control unit to adjust the rotation speed
– safety protection for rotary drum rotation screwed to the structure
- Separator with its own MB WAVE CONTROL panel for adjusting the rotation speed of the drum
- Drum bearing frame supported by two threaded rods allowing drum tilt to be adjusted on both sides, while adjustment in height is facilitated by two gas pumps installed on the lower base
- Safety ensured by a rotatory drum protection screwed to the structure
- Separator with inlet and outlet chute in AISI 304 stainless steel sheet
- Motor connection voltage: 400 V / 50 Hz three-phase
OPTIONALS
- Finer-tuned adjustment: ø 50 mm rollers in AISI 304 stainless steel for increased adjustment accuracy of distance H
- Reduced noise pollution: ø 50 mm rollers in AISI 304 stainless steel filled with soundproofing material
- Simultaneous adjustment of the rollers: dedicated device, with 5 mm minimum distance between rollers
- “Safety package”: micro-switch installed on the cover + Skill Control Mono control panel
OPERATING LAYOUT

NOTES
Finding the right ratio between the rotation speed of the drum and its slight inclination, which can be adjusted thanks to the gas pumps installed on both sides of the base, is the key to efficient separation of the product from the sprues.
In view of the particular functional characteristics of this separator, MB recommends that a test be performed at the offer stage using samples of the products and sprues to be separated
STANDARD DIMENSIONAL FEATURES

EXAMPLES OF POSITIONING BESIDE IMM
P1 - POSITIONING IN LINE WITH THE CONVEYOR

- A conveyor is positioned in front of the press chute so as to collect product from the mould and convey it into the SR2 separator.
- The product and sprues are separated inside the rotary drum.
- The different dimensions determine the passage, between the rollers, of the smaller component of the moulding process (usually the product), which drops into the container below, while the larger parts (usually the sprues) are routed outside the separator
P2 - POSITIONING AT RIGHT ANGLES TO THE CONVEYOR

- Solution where, for reasons of space, the separator is positioned square to the loading conveyor.
This reduces the amount of space taken up outside the press to a considerable extent - This solution is completed by installation of a sprue recovery granulator at the separator outlet.
P3 - POSITIONING AT RIGHT ANGLES TO THE CONVEYOR

- Solution similar to the previous one but with features depending on the product storage container dimensions: 800 x 1200 x h 1200 mm
- A granulator installed in front of the outlet chute of the separator completes this system.
- Loading conveyor and separator complete with Polycarbonate guards.
CONFIGURATIONS

SEPARATOR SR - INTERNAL DETAIL OF ROLLER DRUM
- The photo alongside shows the inside of a roller drum formed by 50-mm diameter PVC rollers
- Complete with sprue, the product enters the drum where drum rotation and counter-rotation of the rollers provide the ideal conditions for separating the product from the sprue

SEPARATOR SR - INTERNAL DETAIL OF DRUM WITH SIMULTANEOUSLY ADJUSTABLE ROLLERS
- Note, in the photo alongside, how the special simultaneous adjustment mechanism allows the same distance between all the rollers to be regulated at the same time
- It is important to underscore how this type of adjustment, although faster and more practical, is less accurate and allows 5 mm minimum distance between the rollers

SM SEPARATOR - INTERNAL DETAIL OF PERFORATED DRUM
- The photo alongside illustrates the inside of a perforated drum made of AISI 304 sheet, complete with linear and spiral inserts for movement and channelled advancement of the product
- The diameter of the holes in the drum is fixed and cannot be changed
- The perforated drum can be easily removed from the separator. If the products frequently change and have different dimensions, replacing the drum with another, duly sized version, could be a strategic solution

SEPARATOR SR - INTERNAL DETAIL OF DRUM WITH STEEL ROLLERS
- The inside of a separator with metallic rollers can be seen in the photo alongside
- This solution is proposed when the drum length and, thus, the useful length for product-sprue separation, exceeds 800 mm
- Steel rollers provide the parallelism able to ensure efficient separation
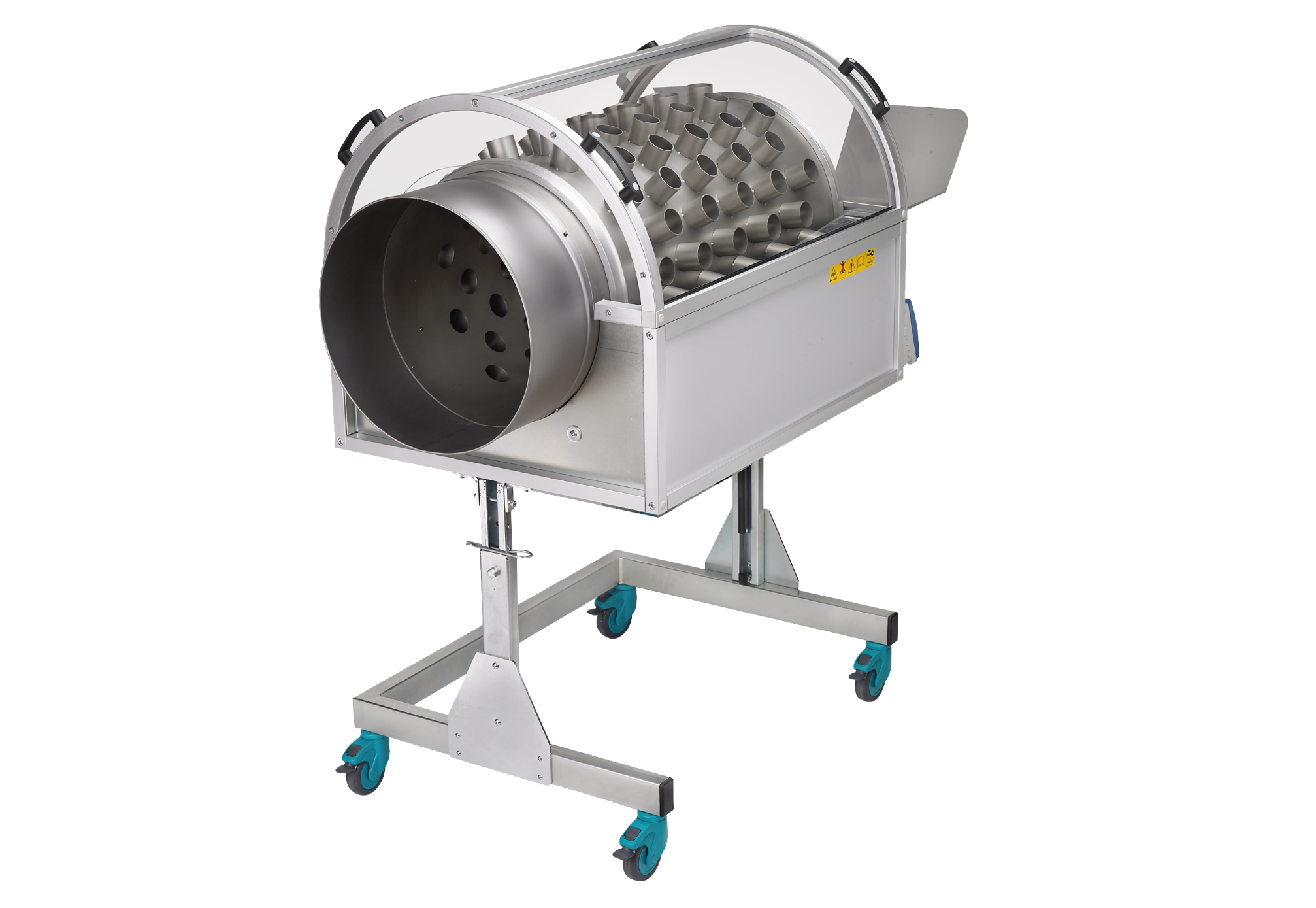
SEPARATOR SM COMPLETE WITH ANTI-ATTACHMENT TUBES
- The solution illustrated in the photo alongside features anti-attachment tubes welded on a level with the holes in the drum
- This prevents the products or sprues from “catching” on the rotating drum and remaining trapped inside it

PRODUCT ACCUMULATION, CONVEYING, SEPARATING AND STORAGE SYSTEM
- The mod. CP 12 conveyor on the press accumulates and conveys the product
- Separator SM receives the product, separates it from the sprue and channels it into the container under the hopper
- A horizontal carousel formed by a PA 110 conveyor + an idle Roller conveyor creates the conditions required for storing the product in the container. The system is controlled by a panel with PLC

SEPARATOR SM COMPLETE WITH ROTATING BELT DISTRIBUTOR
- The solution in the photo alongside allows product separated from the sprue to be stored in several containers under the rotating outfeed belt
- The unloading positions are established by positioning locators in the slewing ring. These positions can be changed as required
- The solution whereby product is unloaded by steps in the same container is interesting since it avoids central heaping and optimizes the filling operation
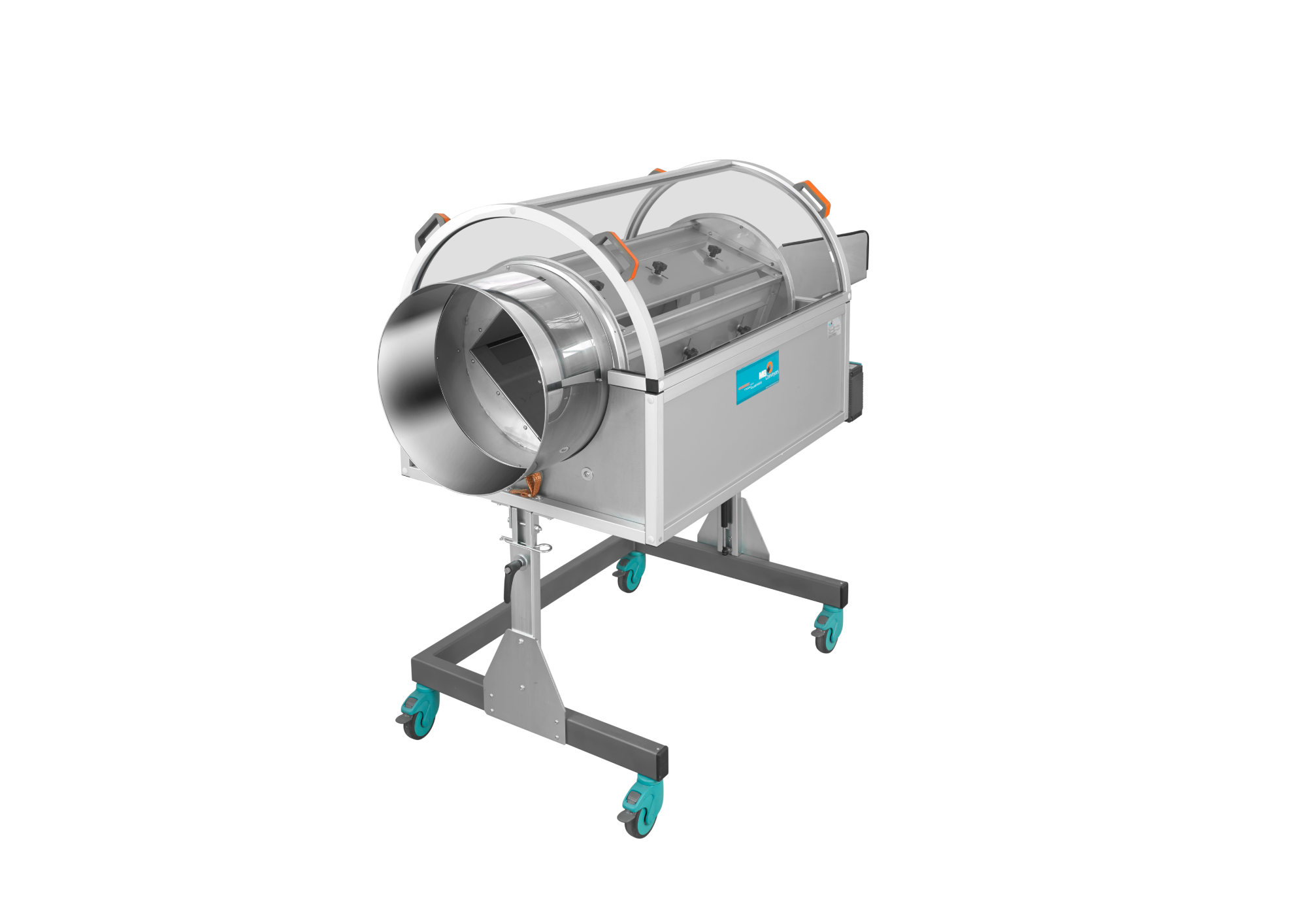
MOD. SQ SQUARE-SECTION SEPARATOR
- In the photo alongside, the separator has a square-section drum. This solution is used when the product has a particular conformation and is very small in size compared to the sprue
- Each side of the drum has an opening regulated by a damper, which creates a very precise and adjustable through-section where separated product is generally released
- Adjustment of the rotation speed of the drum is a key factor for proper separator operation

MOD. SZ SOUNDPROOFED SEPARATORS FOR ALLOY PRODUCTS
- The SZ separator in the photo alongside has metallic rollers and is soundproofed
- The blocks that fix the metal rollers are made of aluminium instead of plastic
- The rollers forming the drum are made of AISI 304 stainless steel and are filled with sound absorbing material
- The soundproofed hood is lined with material with a high capacity for absorbing the noise made by the metallic product

SYSTEM FOR ACCUMULATING, CONVEYING AND SEPARATION FROM THE SPRUE
- The soundproofed hood is lined with material with a high capacity for absorbing the noise made by the metallic product
- Note the conveyor, equipped with a metal damper and coupled to a soundproofed separator
- Use in the metal alloy moulding industry is one of the main applications for these systems
Category: Separation